A Comprehensive Overview of 3D Scan-based Modeling
In the fascinating world of 3D modeling, 3D scan-based modeling has solidified its position as a potent method. Leveraging specialized scanning technologies and cutting-edge software programs, 3D modelers can now create complex 3D replicas of physical objects. This article will explore the fundamental concept of scan-based modeling, its differences from common modeling techniques, and its benefits for 3D design
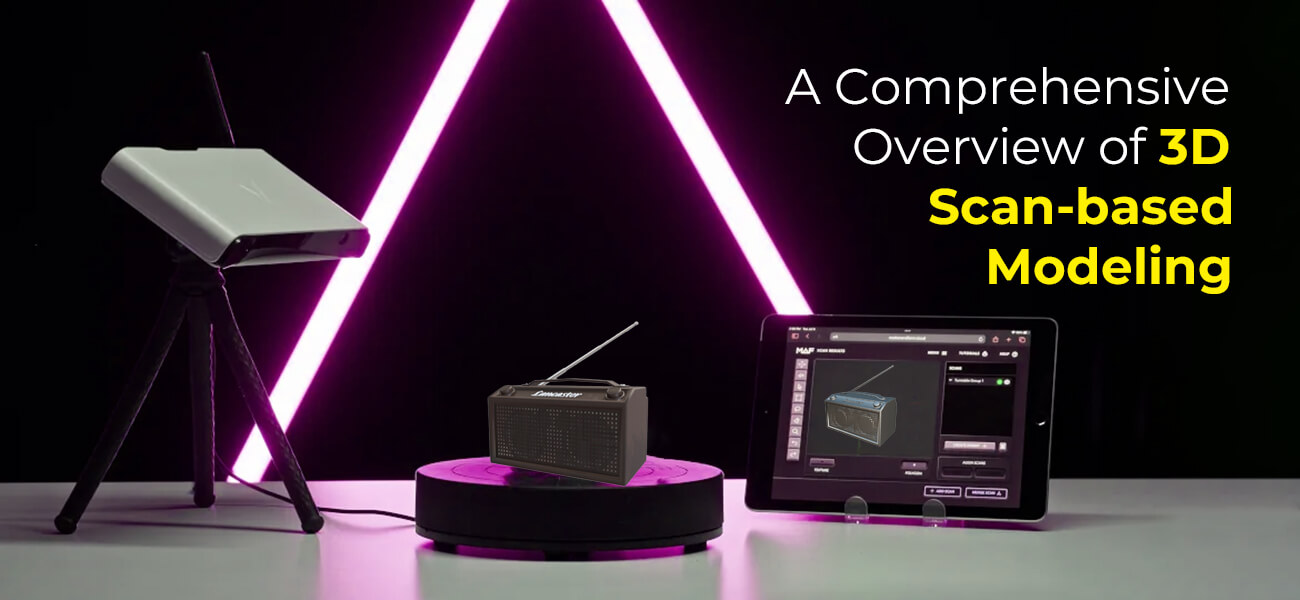
So, whether you are an experienced 3D modeler or an aspiring enthusiast, this article will be your roadmap. Embark on this exciting journey and gain the knowledge to master the art of 3D scanning. Let’s start!
What is the scan-based 3D modeling technique, and how does it work?
It is an advanced process of creating digital models by analyzing 3D data analyzing real-world objects or environments. These data include, shapes, colors, materials, textures, surfaces, and the like. 3D scanning technology is the basis of this novel modeling process.
The entire data analyzing process happens in specialized software programs that capture the geometry and parameters of the specific physical object. Thereby, the digital representation is generated that can be enhanced, refined, manipulated, and finally rendered through other computer software designed for these.
The scanner-based modeling process typically works in a few sequential steps. They are as follows:
Initial 3D scanning: As the name suggests, the procedure starts by capturing a physical object or environment with a 3D scanner. Technologies such as structured light scanning, laser scanning, or photogrammetry are implemented to capture the texture and geometry of the objects precisely.
Collecting data points: The next step is collecting or acquisition of data points from the real-world object’s surface. The 3D scanner executes this precise process of data acquisition to generate a mesh structure representing the object’s geometry and parameters scanned in the first step.
Mesh creation: In this step, the mesh structure or surface model is created by processing the raw data. The raw data is further cleaned and decluttered, and noise and artefacts are refined and optimized. This is done to make the digital mesh suitable for further editing and manipulation.
Refining and enhancing the mesh model: Now, the digital model is imported into another modeling program for further iteration, manipulation, and enhancement. Modelers can adjust the mesh topology, add or eliminate details, and adjust it to give the desired look and feel of the final 3D model.
Texture-mapping: This step involves applying the captured textures, if any, on the surface of the digital model through the texture mapping technique. The texture and color information is usually captured during the initial scanning process and can be mapped on the model. Texture mapping is done to augment the realism of the virtual model, making it appear 100% natural.
Final editing and post-processing: Once the digital model is finished and all the texture maps are added, the final 3D file undergoes a final post-processing step. This is comprised of UV unwrapping, i.e., applying UV maps or projecting 2D images on the surface of the model, rigging, rendering, or animating, depending on its intended usage and application.
Difference between scanner-based 3D modeling process and other digital modeling techniques
Professional 3D modelers utilize various modeling techniques that are significantly different from 3D scanning. Such as surface modeling, solid modeling, polygonal modeling, and more. Each has its own advantages and approach. In this section, we will discuss the key differences between scanned 3D modeling and other 3D design techniques.
-
Data acquisition process
-
Scan-based 3D design:
- Real-world data from physical objects is collected by specialized 3D scanners.
- The scanners capture millions of data points having the objects’ physical geometry and parameters.
- The captured 3D data is analyzed, and accurate digital representations are formed.
-
Other modeling methods:
- Relies on manual inputs to create 3D models from scratch.
- Methods like NURBS modeling, B-spline modeling, polygonal mesh modeling are implemented by the artist.
- The model’s geometry is then formed based on the design specifications.
-
-
Efficiency of the process
Scan-based 3D design:
- Significantly reduces the time taken and resources required to create complex and intricate models.
- Automated 3D data acquisition process eliminates the requirement for manual modeling.
- Reduces efforts to a great extent, thus expediting TAT.
Other modeling methods:
- Requires more time, effort, resources, and production costs to create detailed 3D models.
- 3D modelers have to spend long hours creating the mesh structure from scratch and scupting details.
- Texture application takes the most time, especially for high-end 3D models with minute detailing.
-
Level of realism and design accuracy
Scan-based 3D design:
- Excels in capturing real-world physical objects along with their accurate realism and traits.
- Closely resembles the real-world counterparts by capturing their physical parameters and geometry.
- Ideal for applications where the digital models are required to be precisely accurate.
Other modeling methods:
- Lacks the high level of detailing and realism that a 3D scan-based model can offer.
- Modelers need to manually texture or sculpt the models to yield realism and detail.
- Too much time-consuming and resource-intensive.
-
Versatility and flexibility
Scan-based 3D design:
- 3D scanned models are highly versatile and flexible and can be easily repurposed for various applications.
- Hassle-free editing, manipulating, and refining process through standard 3D modeling tools.
- Compatible with existing project workflows and pipelines.
Other modeling methods:
- Not as flexible or adaptable as the 3D scanning process.
- Design topology or geometry manipulation, especially for intricate models, requires significant rework.
- Lengthy refining and alteration process; labor-intensive.
-
Usages and applications
Scan-based 3D design:
- Widely used in business sectors like media and entertainment, film, product design, construction, reverse engineering, etc.
- Ideal for applications requiring accurate digital replicas of physical objects or environments.
- Used for digital 3D printing and prototyping as well, scanning a physical product into STL format.
Other modeling methods:
- Mainly used for architectural visualization, character design, animation, 3D assets creation, game environment creation, industrial design, etc.
- Offer creative freedom and control but require more manual effort.
- Difficult to achieve 100% realistic results, considering the models focus solely on geometrical patterns and not on the physical traits of real-world objects.
Although the 3D scanning process and other modeling methods share a common goal of generating 3D models, they have the above fundamental differences. Having a thorough understanding of these differences can help 3D professionals apply the right approach for specific project requirements.
Professional agencies have skilled 3D experts who are the right judge of which technique to apply for which project. This is why it is always best to work with experienced 3D service providers.
Types of 3D scanning or scan-based 3D modeling
Several scan-based modeling types are there, each having its own advantages and applications across major industries. Most experienced 3D designers are fluent in these 3D scanning techniques. Let’s check them out.
-
Photogrammetry
A technique where a series of overlapping photographs of the physical object is used to reconstruct its geometry. The scanner tool analyzes the common physical traits and perspectives of the real-world object or environment. The photogrammetry software can then calculate the orientation and positioning of each 3D data point.
This technique is mostly used for large-scale project demanding lots of precise, calculated measurements, like environmental monitoring, surveying, aerial mapping, etc.
-
Laser scanning
It is a unique 3D scanning technique that works by emitting laser beams on the physical object’s surface and then by measuring the time taken for the beams to reflect back to the scanner. This technique is best for capturing detailed and accurate physical geometry of real-world objects and environments. The laser beams capture millions of data points, thereby forming a detailed point cloud that can be processed into a digital replica.
This method is well-suited for purposes like cultural heritage preservation, product design, plan renovation, construction, identifying design flaws, etc.
-
Time-of-Flight scanning
This is another scanning technique where the scanner emits light pulses and measures the time taken by the light signal to travel to the object and reflect back to the scanner. The ToF scanner measures the distance of the light reflection to each point on the surface of the object.
This technique is quite efficient and is thus suitable for applications like industrial inspection, MRA scanning, the automotive industry, driverless vehicles, and so on.
-
Structured light scanning
In this technique, structured light scanners project a pattern of light on the real-world object’s surface and capture the pattern deformation using cameras. Thereafter, the scanners analyze these patterns distortions and accurately reconstruct the 3D geometry of the object.
The structured light scanning method is ideal for capturing natural textures and fine details; therefore, it is mostly used for creating character animation, lifelike CG graphics, forensic analysis, reverse engineering, etc.
-
Contact scanning
This particular scanning method involves pobing the real-world object’s surface with a touch sensor to capture its physical parameters. This process is more invasive than other other techniques mentioned above. The software embedded within the sensor records how and where the probe touches the object’s surface and records the 3D surface location.
As unusual as it seems, this technique is best for quality control, reverse engineering, metrology, manufacturing, etc.
-
Multi-sensor fusion
This technique is a mix of a few other scanning methods discussed above, namely, photogrammetry, structured light scanning, and laser scanning. Hence, it captures greatly accurate and precise 3D data points. It goes without saying that the 3D information collected in this process fusing some of the most crucial scanning methods, is 100% accurate.
That said, the level of accuracy and resolution achieved with this technique is much higher than any other method used individually. This is mostly used for creating models that ought to be highly detailed, accurate, and have natural-looking textures. For AR-VR, digital preservation, SLAM systems based on 3D LIDAR, etc.
To sum up this segment, all these various types of 3D scanning methodologies are unique by themselves. Knowing each of these is a must-have skill for any digital modeler, product designer, researcher, new-age medical professional, and the like. Based on their specific needs and objectives, they can apply the respective method for visually stunning model creation.
Benefits of 3D scanning for creating 3D models
3D scanning has multifaceted benefits for modelers in terms of efficiency, precision, and versatility. By wielding the specialized 3D scan-based modeling software and tools, 3D designers can unleash the true potential of this advanced digital modeling technology. The following are the benefits offered by this sophisticated 3D design method:
-
Offers exceptional realism
This is probably one of the key benefits of 3D models from the scan base enjoyed by most industries. 3D professionals can capture the accurate realism of physical objects with photogrammetry or laser scanning, thereby creating hyper-realistic models.
These high-fidelity models are ideal for applications where realism is paramount, such as medical imaging, cultural heritage preservation, etc.
-
Helps to reduce production costs
The 3D scanning method significantly lowers production costs involved in developing high-detail 3D models, especially for complex organic shapes. Traditional modeling process requires many resource-intensive and expensive steps, such as CAD modeling, or manual sculpting.
This also makes the entire thing quite time-consuming. Whereas, scan-based 3D design is more automated eliminating the need for manual intervention for creating 3D wireframes or adding intricate details.
-
Fosters team collaboration
Scan-based modeling fosters productive team collaboration and cross-departmental communication more than any other method. The process generates accurate digital representations that provide immense clarity to all the stakeholders involved. Right from the customers, to investors, sponsors, team members, and collaborators, everyone can understand a common visual language.
This streamlines communication, lessens misinterpretations and misunderstandings, and keeps everyone on the same page. The process also facilitates remote collaboration and feedback exchange regardless of the distance.
-
Ideal for documentation and preservation
This process is best known for playing a vital role in preserving and documenting of artefacts, historical monuments, archaeological sites, sculptures, ancient scriptures, and more. Developing exact digital replicas of these artefacts helps in preserving valuable cultural heritage for future generations.
It also provides historians, researchers, and conservationists valuable resources for research, analysis, and restoration purposes.
-
Immensely flexible for manipulating, editing, and refining
Scanned 3D models are exceptionally flexible and offer versatility in relation to editing, manipulating, and refining the models. As well as for repurposing them for various applications and purposes. The scanned and converted digital model can be customized to the desired effect by adding or removing details. 3D artists can also combine multiple scanned files to create one composite model.
All this flexibility and versatility make scan 3D modeling a perfect tool for product design, forensic analysis, media and entertainment, architecture, and more domains.
Wrapping up
There you are! It’s an official wrap to our comprehensive guide to the 3D scan-based modeling process. Hope this insightful resource has provided the readers with adequate knowledge about this transformative 3D modeling technology. Simply put, the 3D scanning method offers unparalleled precision, accuracy, and flexibility to 3D artists and digital creators across the globe.
Given these practical benefits, this particular 3D design process has been adapted to several business sectors and industries.
The future will see much more advancements and research in this field opening more doors to creative expression. It is high time product manufacturers, researchers, medical professionals, and 3D artists embrace this method of developing 3D models. Several experienced service providers are there offering top-notch 3D modeling services. Collaborating with expert 3D modeling companies is the best way to get world-class scan-based 3D modeling services.